Why does the hexagon bolt need to be black oxide?
Hexagon bolt blackening treatment can play the role of rust prevention and beauty. Commonly used are Black oxide, phosphating, black zinc plating.
Hexagon bolt black oxide treatment
Fastener Black oxide is a common method for chemically anti-rusting the surface of fasteners. The main principle is to produce an oxide film on the entire surface of the fastener through a chemical treatment to isolate the air and prevent the surface of the fastener from contacting air, thereby achieving the purpose of rust prevention.
Black oxide treatment can be used when the appearance requirements are not high. The surface blackening treatment of steel parts is also called bluing.
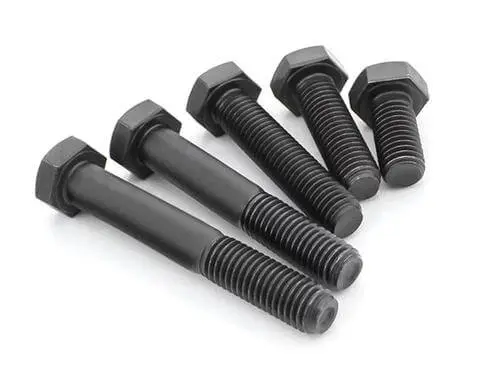
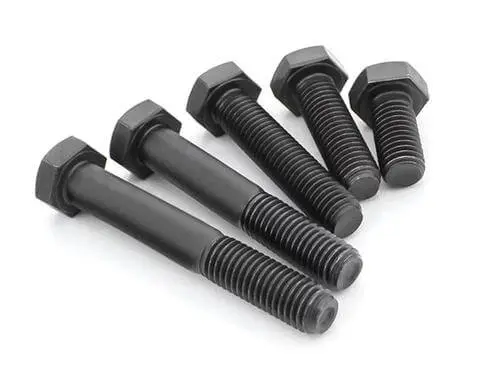
Phosphating treatment
The main purpose of phosphating treatment is: to provide protection to the base metal and prevent the metal from being corroded to a certain extent; it is used as a primer before painting to improve the adhesion and anti-corrosion ability of the paint film layer; in the metal cold working process Play the role of anti-friction and lubrication.
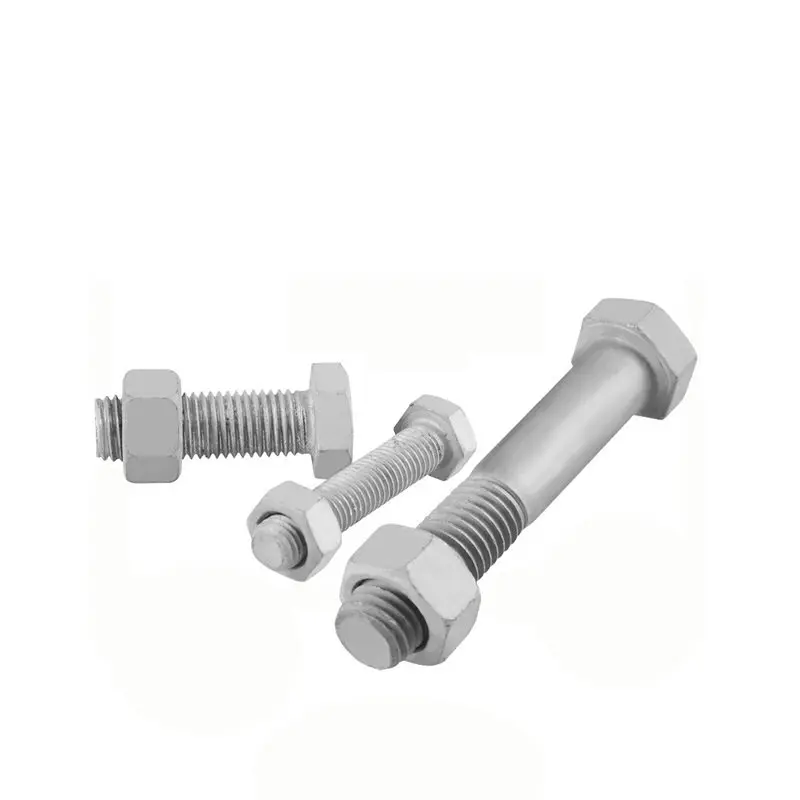
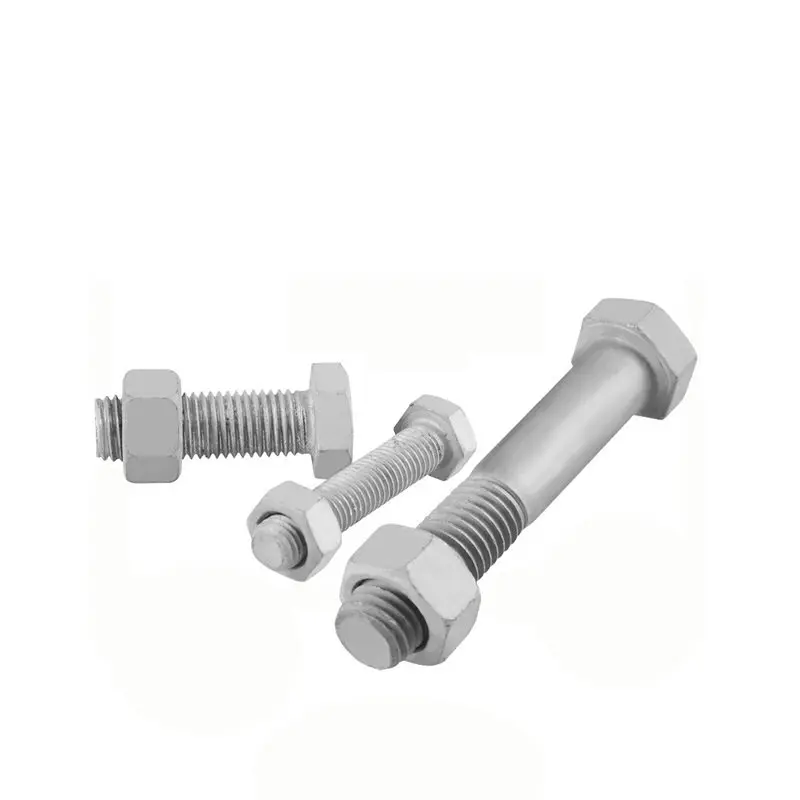
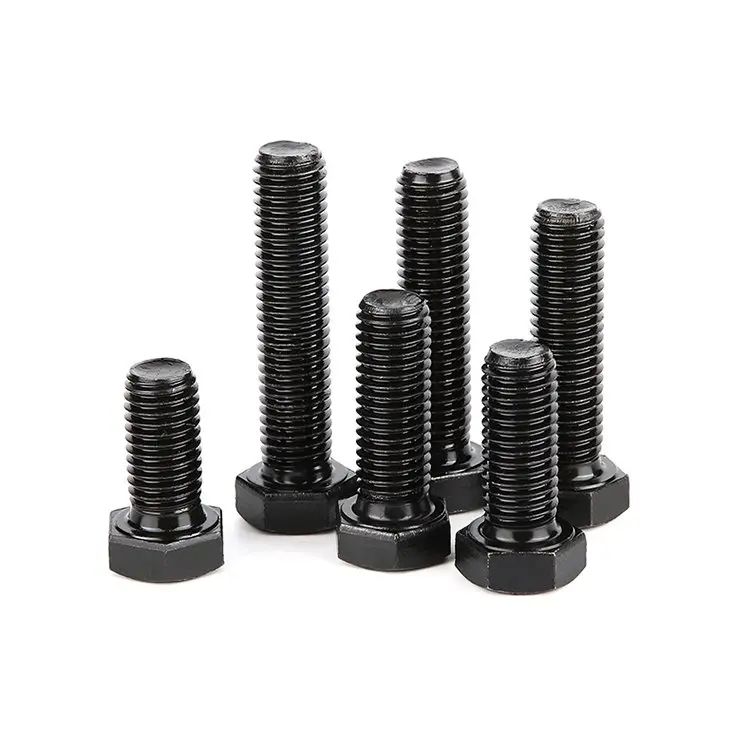
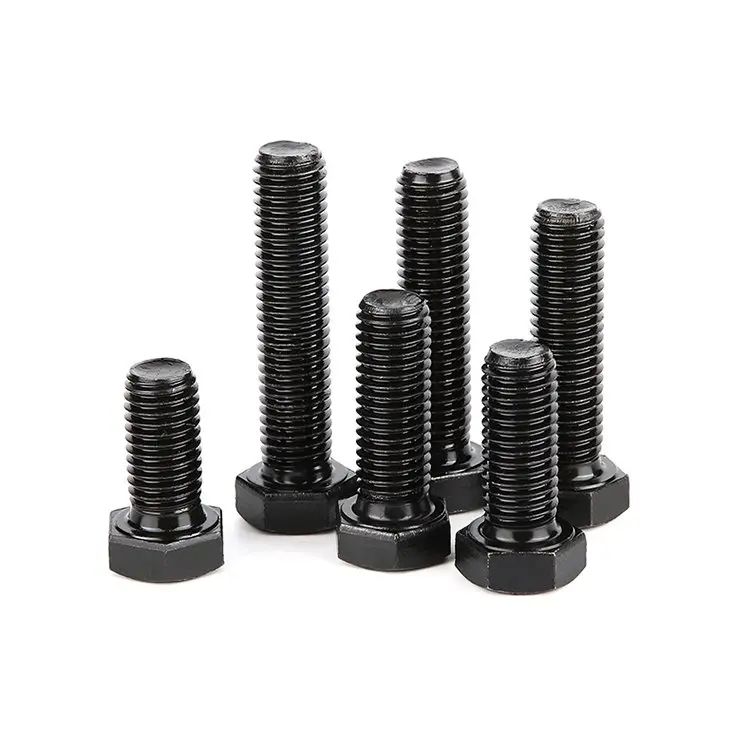
Brief introduction of high-strength hexagon bolt:
High-strength hex bolts are high-strength bolts, which belong to a standard part. Under normal circumstances, high-strength bolts can bear a greater load than ordinary bolts of the same specification. The construction of high-strength bolts must be first tightened and then finally tightened. For the first tightening of high-strength bolts, an impact type electric wrench or torque adjustable electric wrench must be used; and the final tightening of high-strength bolts has strict requirements, and the final tightening of torsion shear-type high-strength bolts must use torsion shears. Torque-type electric wrenches must be used for final tightening torque-type high-strength bolts.
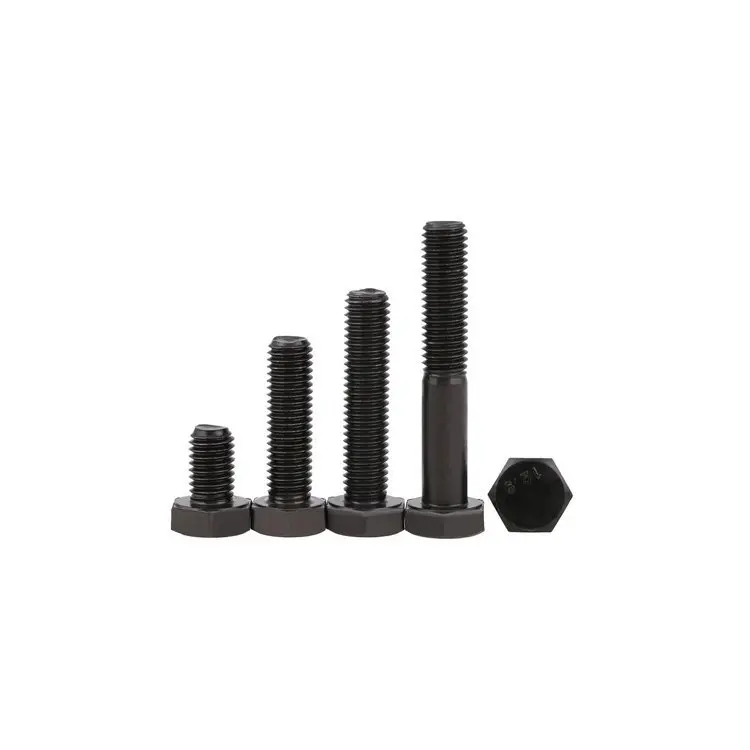
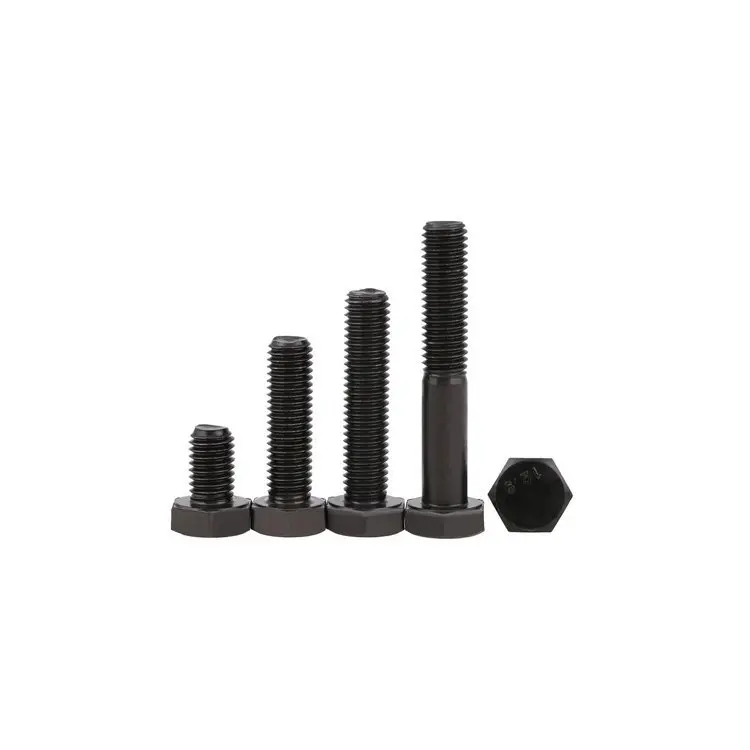
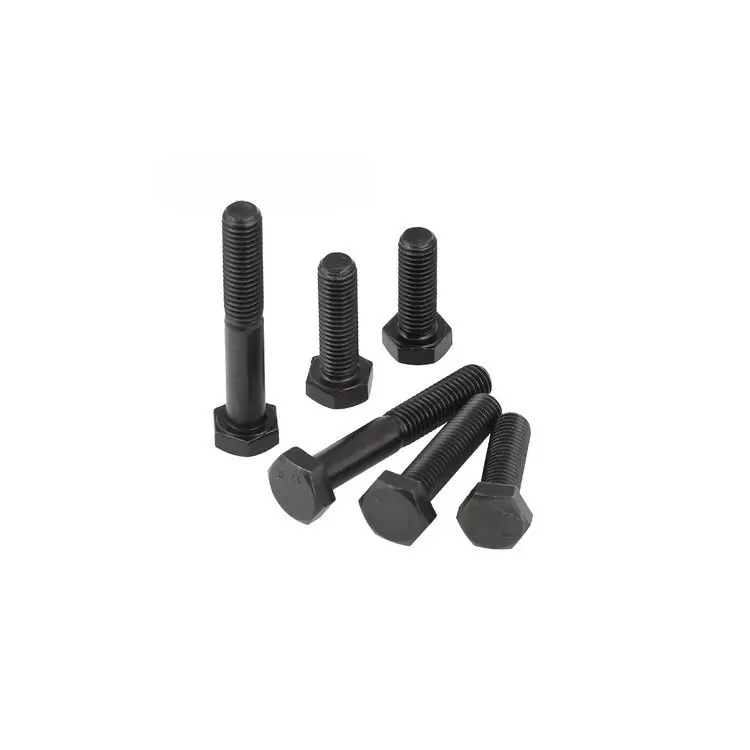
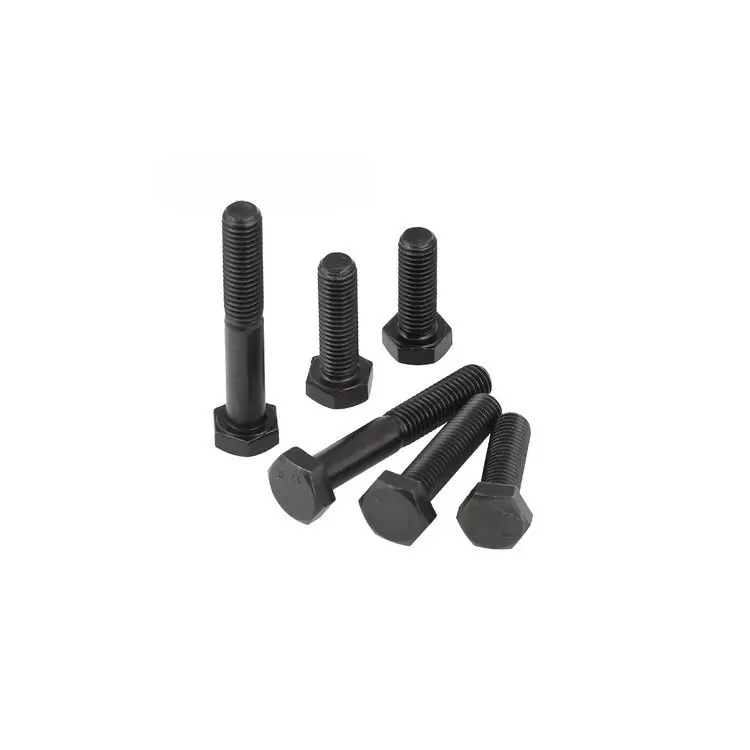
Why do ordinary hexagon bolt need to be galvanized, but high-strength hexagon bolts are black oxide
High-strength bolts are generally used in important connection parts, subject to greater tensile and shear forces. The last process in bolt processing is heat treatment, commonly known as quenching, to increase the strength of the bolt. The bolts are prone to hydrogen embrittlement during the galvanizing process. Hydrogen embrittlement usually manifests as a delayed fracture. This will reduce the strength of high-strength bolts. Therefore, the black surface layer produced during the reheating treatment of high-strength bolts is a relatively stable oxide film. Generally, it will not rust when not in contact with corrosive substances.
High-strength fastener gaskets are prone to hydrogen embrittlement if they are phosphate, and the blackening agent is oxidized into the water in the blackening tank due to the strong oxygen agent.
In fact, high-strength bolts are also phosphates in large quantities. The hydrogen embrittlement problem of phosphating is no longer a problem. There are two ways to deal with hydrogen embrittlement.
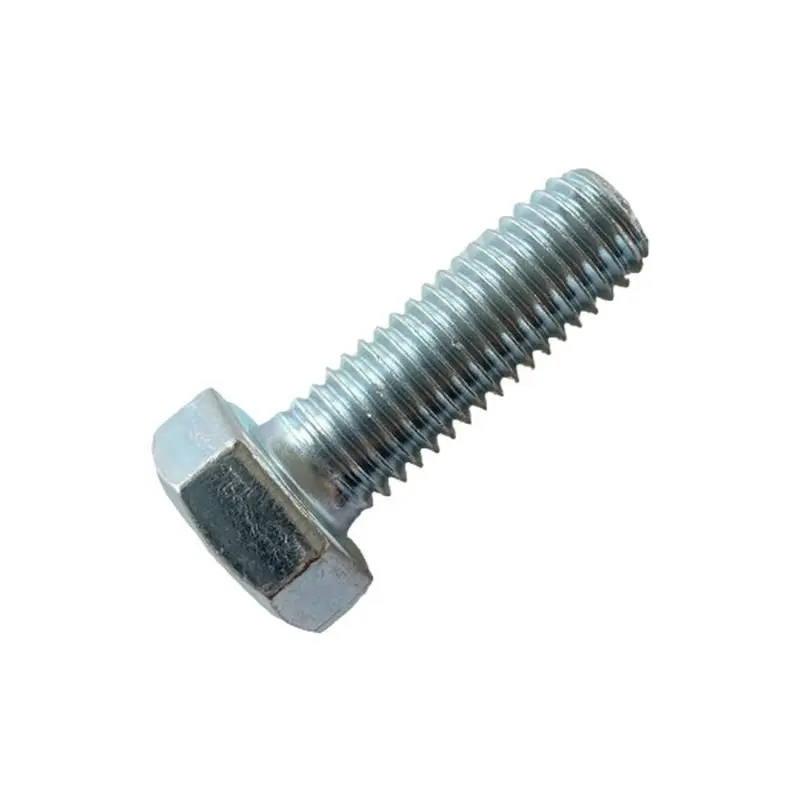
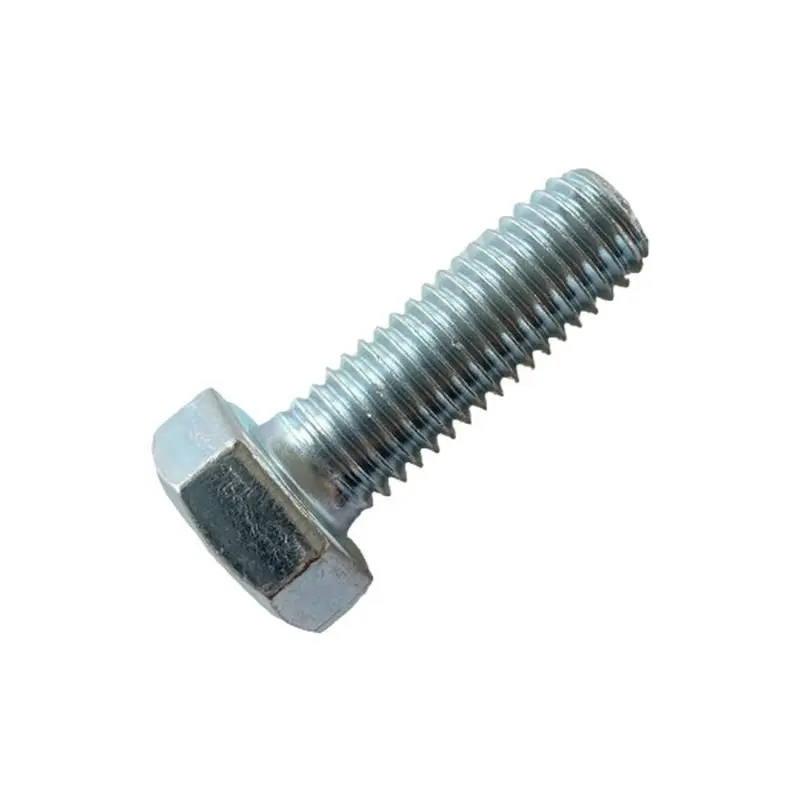
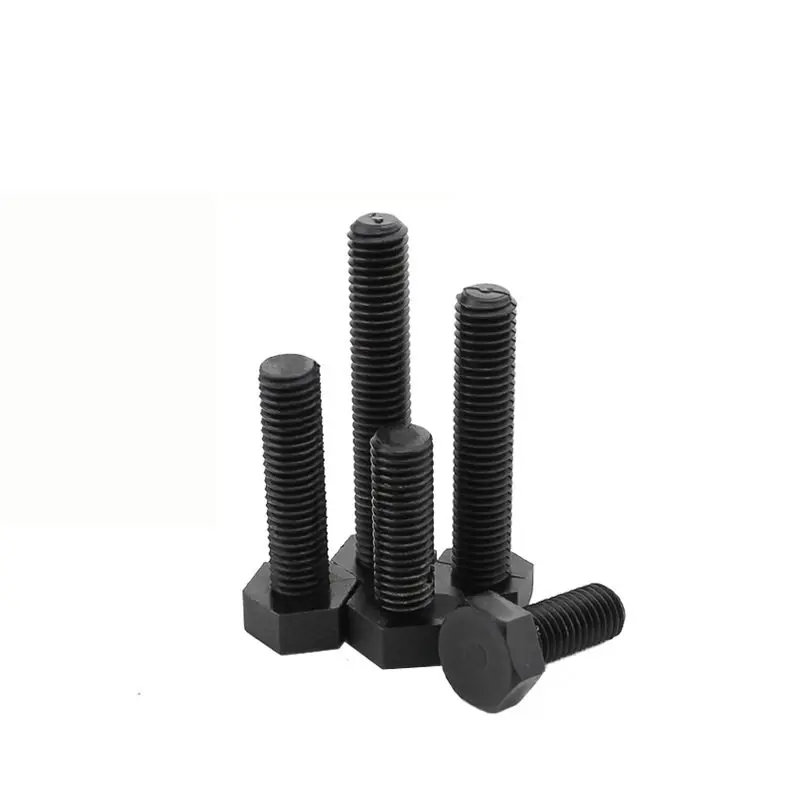
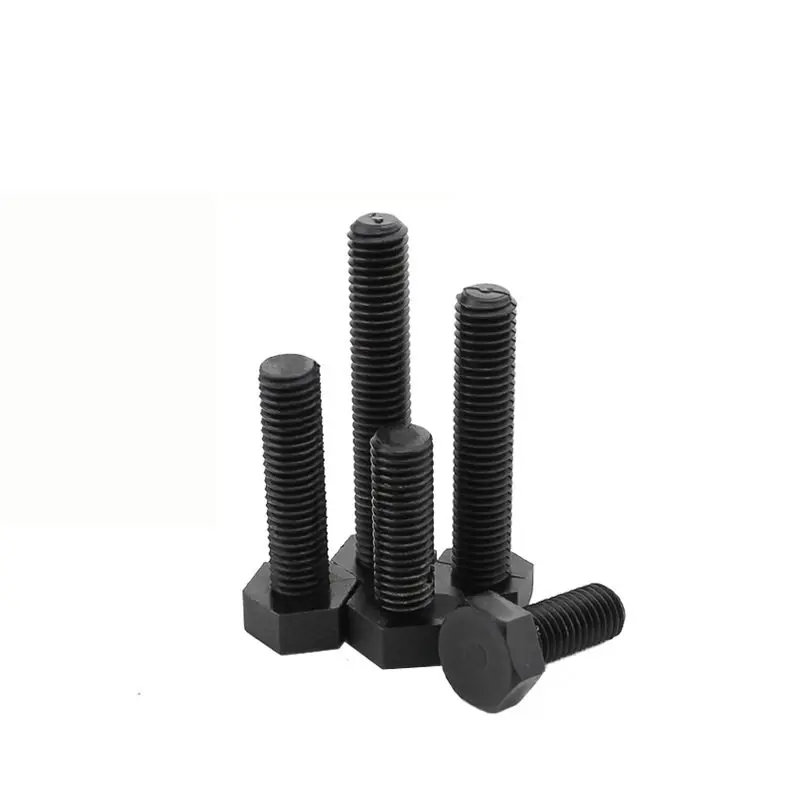
Physical removal of hydrogen
that is baking at 180 degrees for 4 hours, but the damage to the phosphating film is severe. At this time, the crystal water of the phosphating film will lose two, and the structure of the phosphating film will become loose. Has a greater impact on corrosion resistance.
The chemical removal method
that is, after the workpiece is pickled, the chlorine ions are oxidized into water with a strong oxygen agent, and then phosphatized. But this development has not been generally recognized by the industry. But the actual effect is very good. We have done the phosphating of high-strength fasteners and auto parts standard parts for 9 years, and there has never been hydrogen embrittlement.
Hexagon bolt grade
Bolt performance grades are divided into many grades, like ordinary bolts are 3.6, 4.6, 4.8, 5.6, 6.8, high-strength bolts are 8.8, 9.8, 10.9, 12.9, and bolts of 8.8 and above are made of low-carbon alloy steel or medium-carbon steel, and are heat-treated (quenched, tempered) Fire), commonly known as high-strength bolts, and the rest are commonly known as ordinary bolts.
The bolt performance level is described by two-part labels, which respectively indicate the requirements of the standard tensile strength value and the yield strength value of the bolt material.
The mechanical performance requirements of grade 4.6 hexagon bolt
1. The standard tensile strength value of the bolt material must reach 400MPa;
2. The yield strength value of the bolt material must reach 0.6;
3. The standard yield strength value of the bolt material reaches 400×0.6 = 240MPa
Performance grade 10.9 high-strength hexagon bolt, after heat treatment, the material can reach
1. The standard tensile strength value of 10.9 bolt material must reach 1000MPa;
2. The yield ratio of the bolt material is 0.9;
3. The nominal yield strength of the bolt material reaches 1000×0.9=900MPa
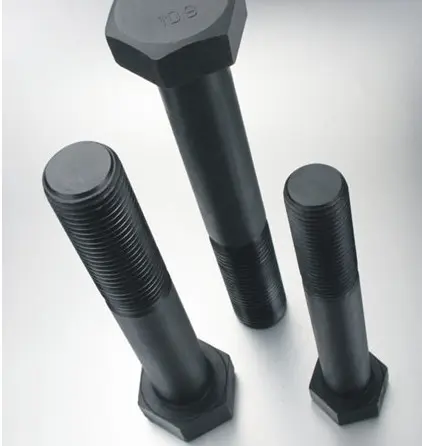
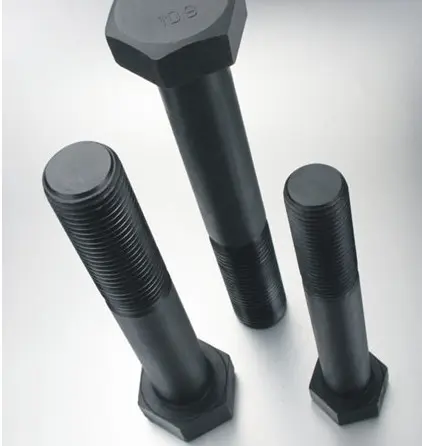
The meaning of the bolt performance grade is the international standard. Regarding bolts of the same performance level, we should not pay attention to the origin of the raw materials, because the raw materials are now produced in large factories, with fewer impurities, qualified ingredients, and fully qualified mechanical properties. So in engineering design, you only need to select the performance level of the fastener.
Choice of fastener surface treatment
Since almost all commercial fasteners are made of carbon steel and alloy steel, some types of fasteners hope to prevent corrosion. Even if the fasteners of corrosion-resistant materials are used, surface treatment is still required to prevent corrosion of different materials. In addition, the plating layer of the surface treatment must be firmly attached and cannot fall off during installation and removal. For threaded fasteners, the plating layer must be thin enough so that the threads can still be screwed after plating. Generally, the limit temperature of the fastener surface coating is lower than the limit temperature of the fastener raw material, so the working environment temperature requirements of the fastener must also be considered in the engineering design. For the surface treatment of fasteners, ordinary people usually pay attention to aesthetics and anti-corrosion. However, fasteners are industrial products whose main function is to fix parts and not process ports. Therefore, the surface treatment of fasteners fully meets the engineering design requirements of fasteners. Therefore, when choosing surface treatment, The factor of tightening performance should also be considered, that is, the consistency of installation torque-pre-tightening force.
Electro-galvanized
Fastener surface electroplating is the most commonly used industrial and commercial fastener coating, It is cheaper and looks good, and it can come in black or army green. However, the anti-corrosion performance of surface electro-galvanization is general, and its anti-corrosion performance is the lowest among all surface treatments and galvanized (coating) layers. General electro-galvanized fasteners do not need to undergo a salt spray test. If testing is required, the price is much higher than ordinary fasteners. The neutral salt spray test of electro-galvanized fasteners is within 72 hours.
Hydrogen embrittlement is likely to occur after electro-galvanizing after tightening, so bolts above 10.9 are usually not galvanized, and the surface treatment is usually blackened or hot-dip galvanized. In reality, the general production plant will not take the initiative to remove hydrogen, unless mandatory requirements of specific customers.
Electro-galvanized fastener torque-pre-tightening force consistency is poor and unstable, generally not used for the connection of important parts
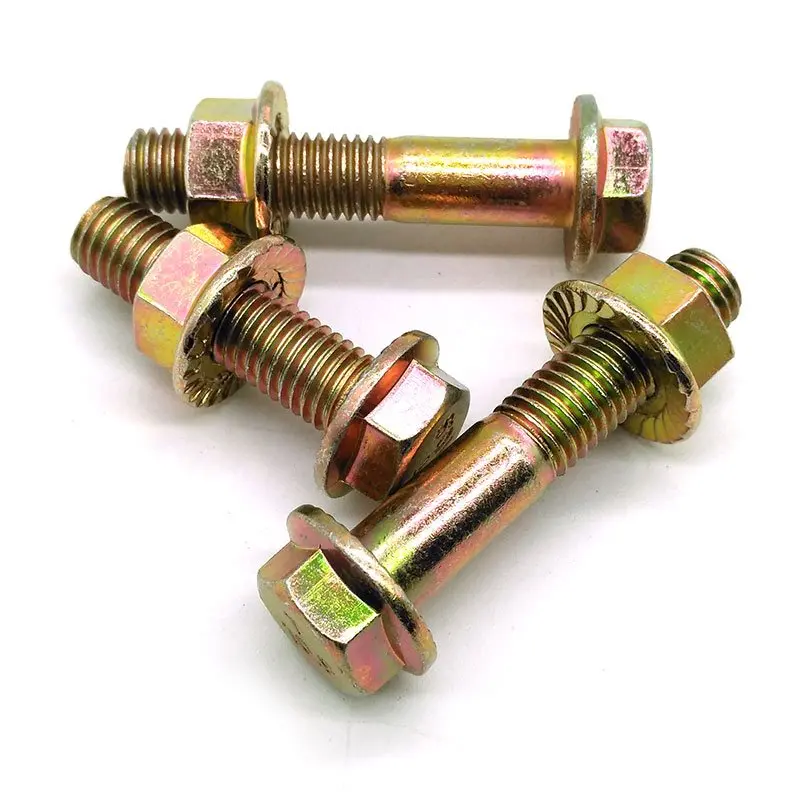
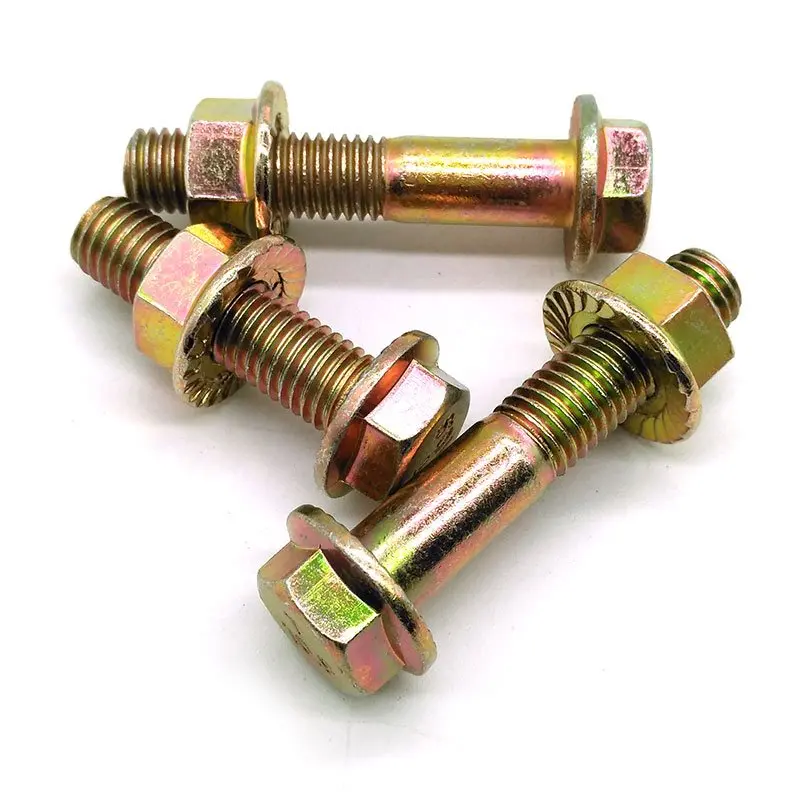
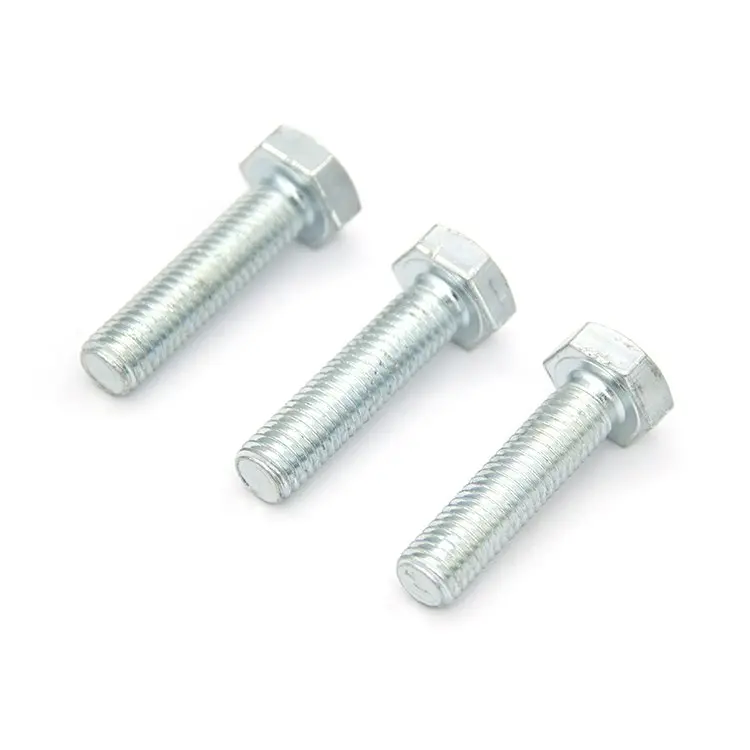
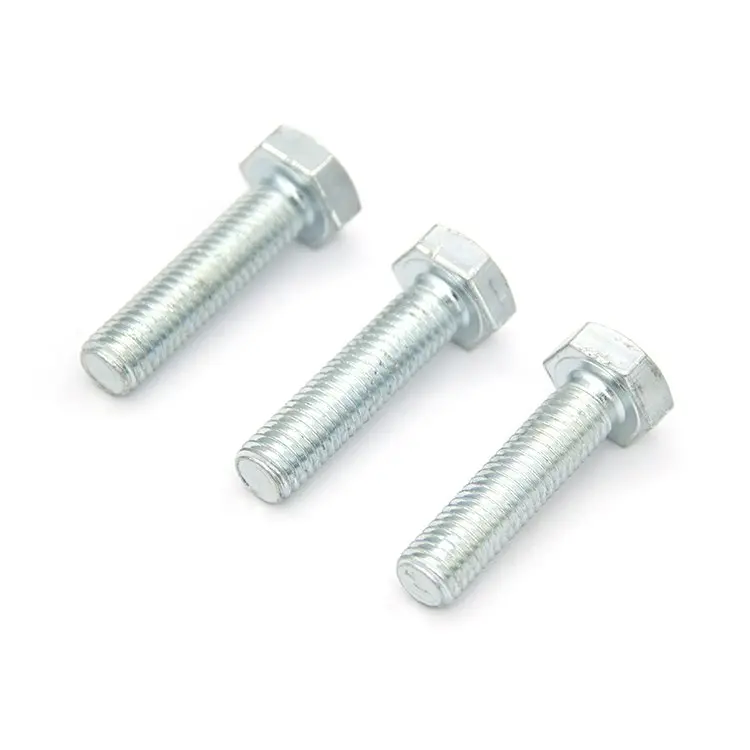
Phosphating
phosphating is cheaper than galvanizing, and its corrosion resistance is worse than galvanizing. Oil should be applied after phosphating. The level of corrosion resistance has a great relationship with the performance of the applied oil. For example, applying general anti-rust oil after phosphating, the neutral salt spray test is only 10-20 hours. Apply high-grade anti-rust oil for 72 to 96 hours. But its price is much higher than that of ordinary phosphating oil.
There are two commonly used fastener phosphating, zinc-based phosphating and manganese-based phosphating. Zinc-based phosphating has better lubricity, corrosion resistance, and wear resistance than manganese-based phosphating. Its working environment temperature can reach 225°F to 400°F (107~204°C).
Many industrial fasteners are treated with phosphating oil. Because it has a good torque-pre-tightening force consistency, it can guarantee to meet the tightening requirements expected by the design during assembly, so it is used more in the industry. Especially the connection of some important parts. For example, the steel structure connection pair, the connecting rod bolts, and nuts of the engine, the cylinder head, the main bearing, the flywheel bolts, the wheel bolts,and nuts, etc.
High-strength bolts are phosphated, which can also avoid the problem of hydrogen embrittlement. Therefore, in the industrial field, bolts above 10.9 grade generally adopt phosphating surface treatment.
Oxidation (black oxide)
Black + oil is an industrial fastener coating that all factories use, mainly because it is the cheapest and the surface coating has an excellent appearance. Since it has almost no anti-rust ability due to blackening, it will rust soon after it is oil-free. When the oil is attached to the metal surface, the time of the neutral salt spray test is relatively short, only 3 to 5 hours.
Blackened fastener torque-pre-tightening force consistency is also very poor. If you need to improve this situation, you can apply grease to the internal threads of the fastener during installation, and then install it.
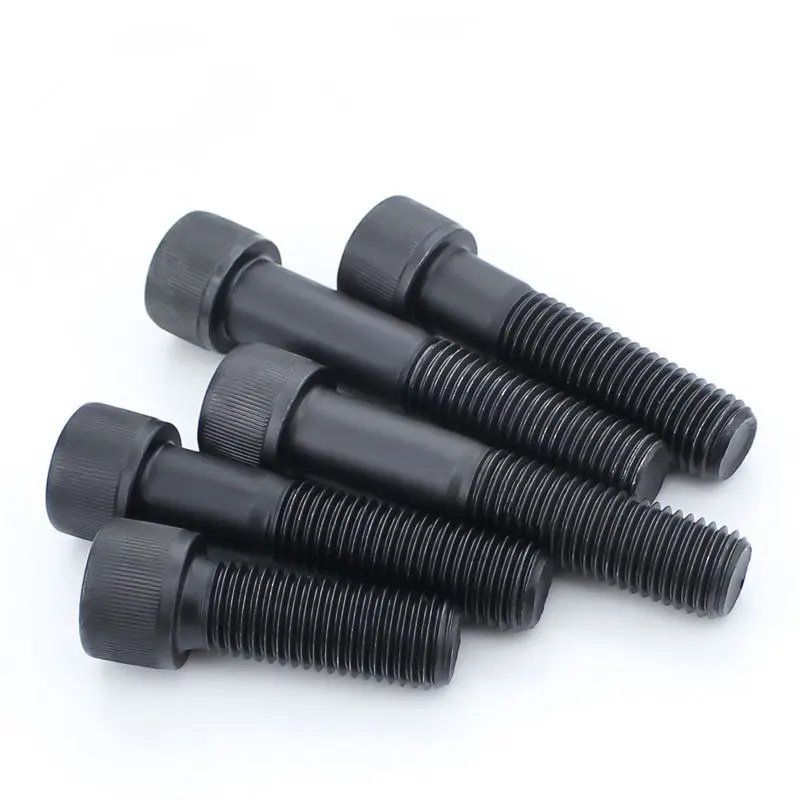
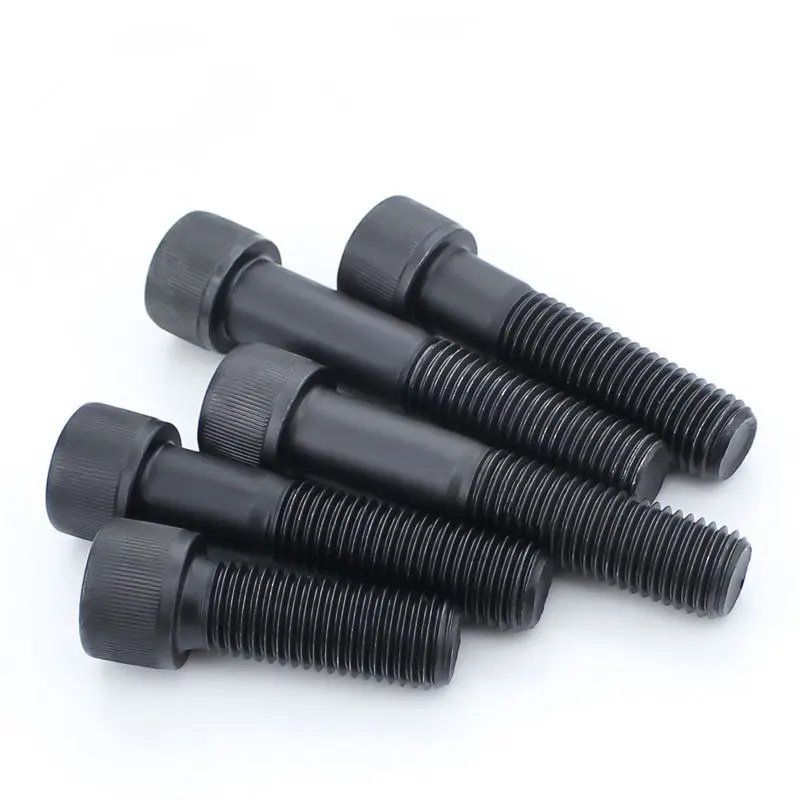
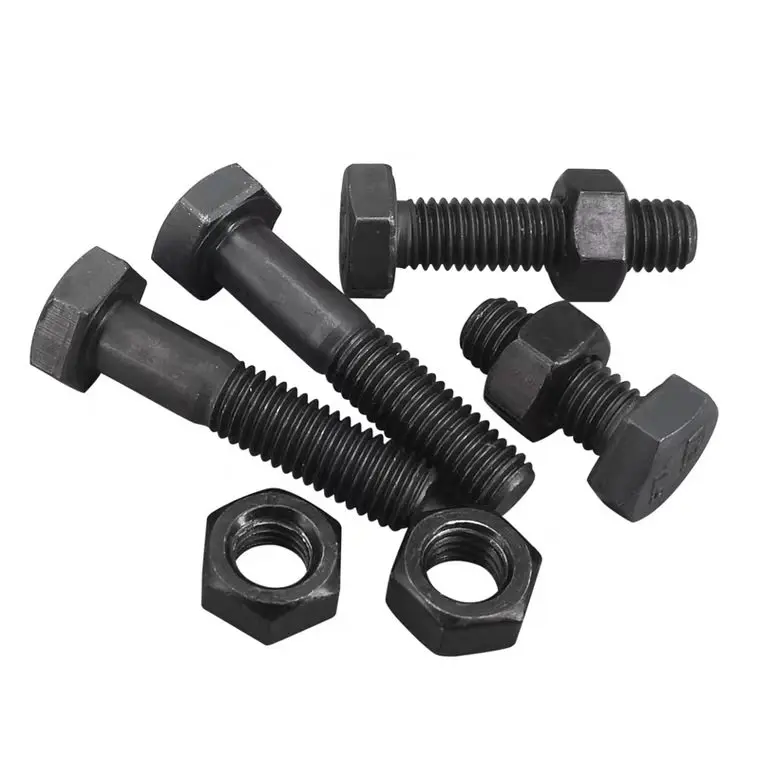
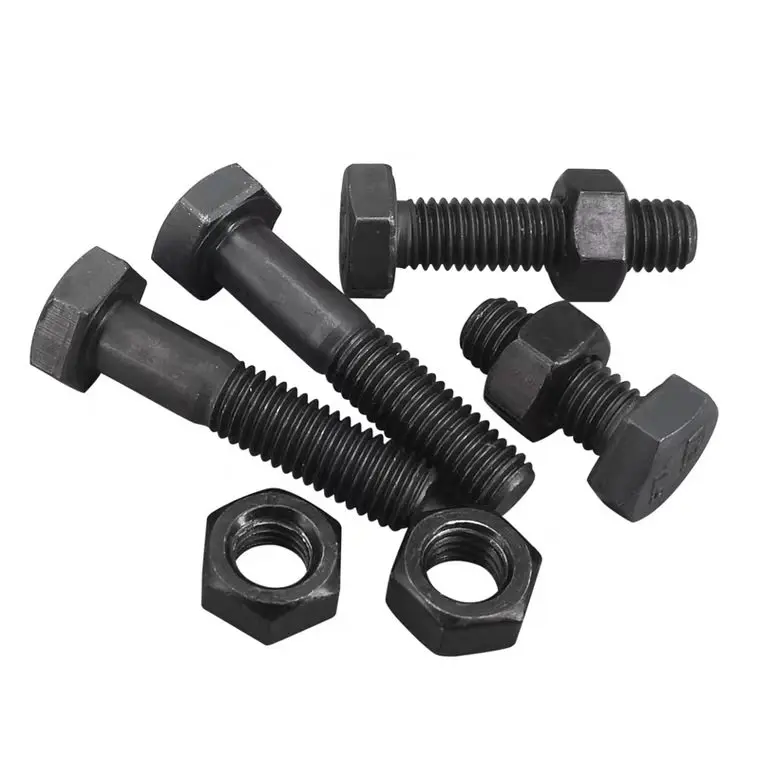
Cadmium plating
The cadmium coating has good corrosion resistance, especially in the marine atmosphere, the corrosion resistance is better than other surface treatments. The cost of waste liquid treatment during the processing of cadmium electroplating is high and the cost is high, and the price is about 15-20 times that of electro galvanized zinc.
Therefore, it is not used in general commercial industries, but only in certain specific industrial environments. For example, fasteners for oil rigs and HNA aircraft.
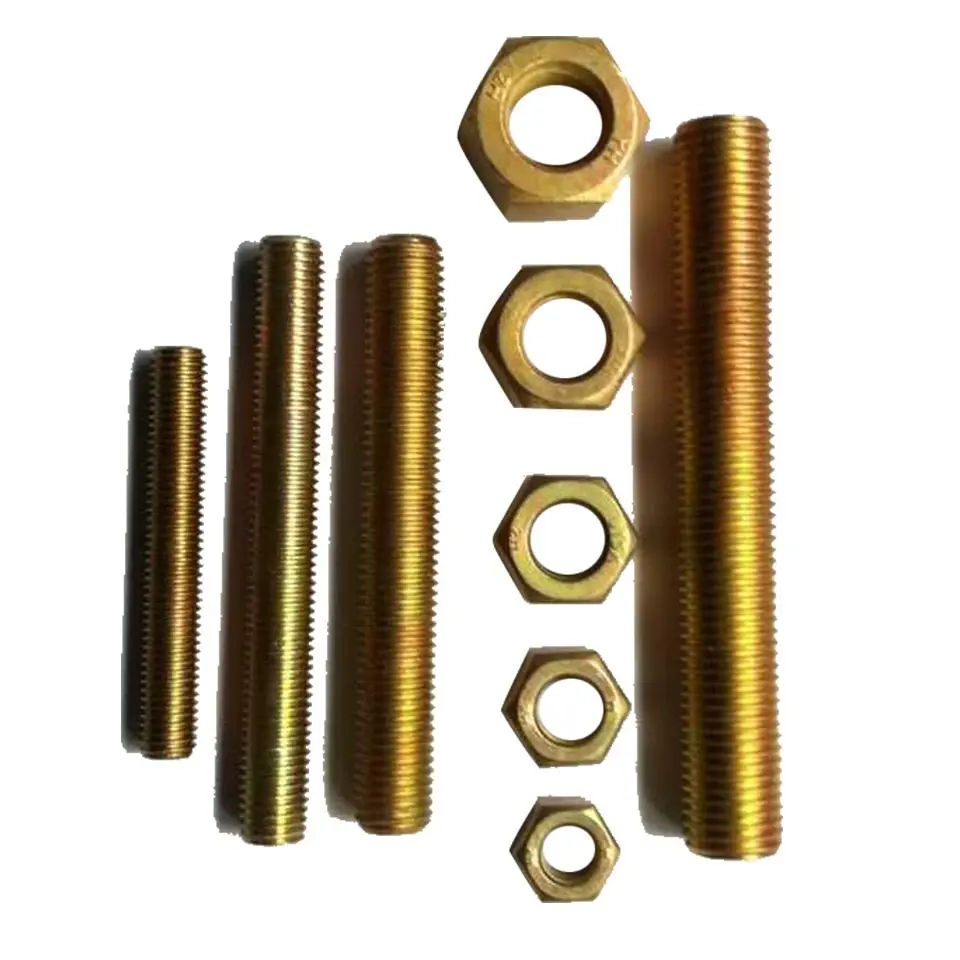
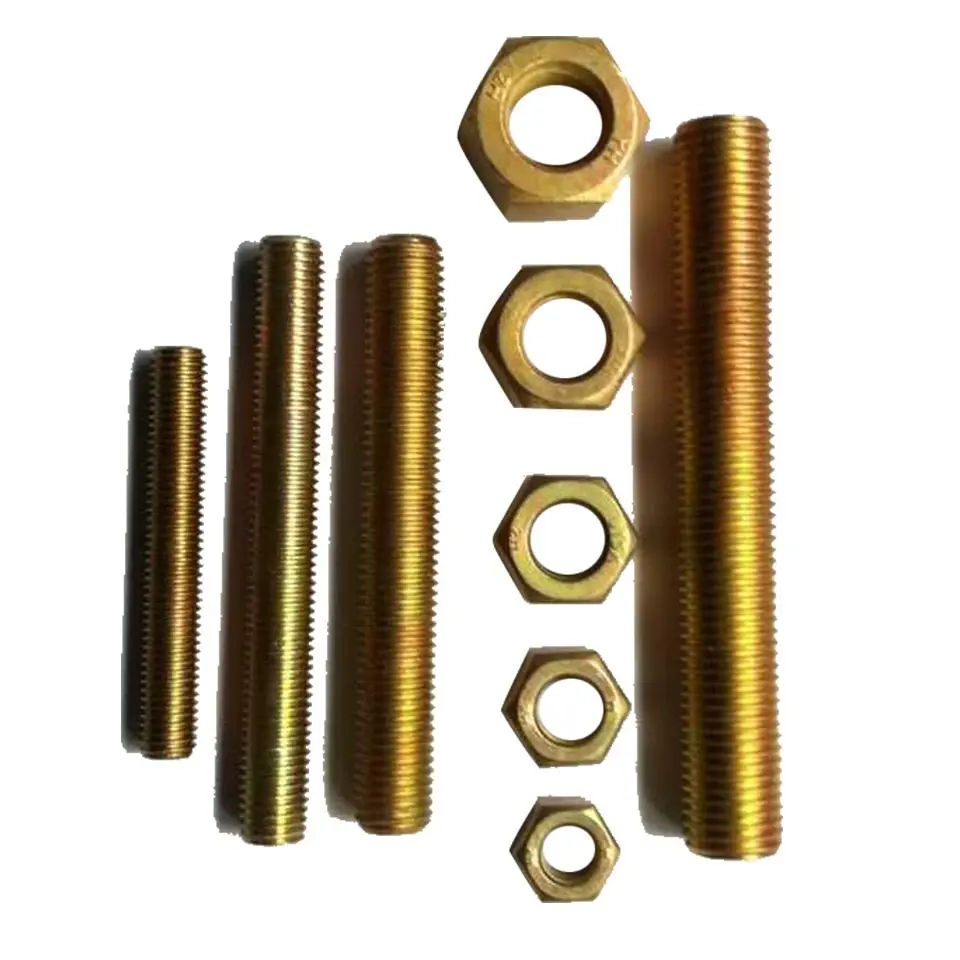
Chrome plating
The chrome plating on the surface of the fastener is very stable in ordinary environments, the color is durable, the gloss is good, the surface hardness is high, and the surface has good wear resistance.
Chrome plating on fasteners is generally used for decorative purposes. In industrial fields with high requirements for corrosive environments, stainless steel fasteners are generally used, because the price of chrome-plated fasteners is as expensive as the price of stainless steel fasteners, but the corrosion resistance of stainless steel fasteners is much better than that of Chrome-plated fasteners, use chrome-plated fasteners only when the strength of stainless steel is insufficient.
In order to prevent corrosion, copper and nickel should be plated before chromium plating. The chromium coating on the fastener surface can withstand high temperatures of 1200°F (650°C). But in a high-temperature environment, it also has the problem of hydrogen embrittlement.
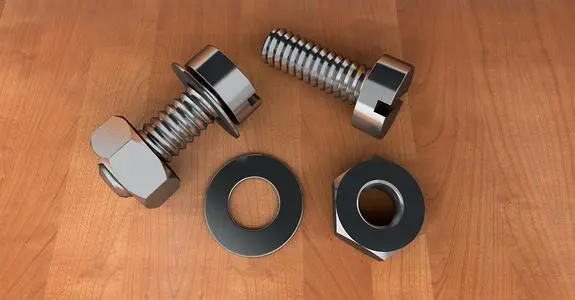
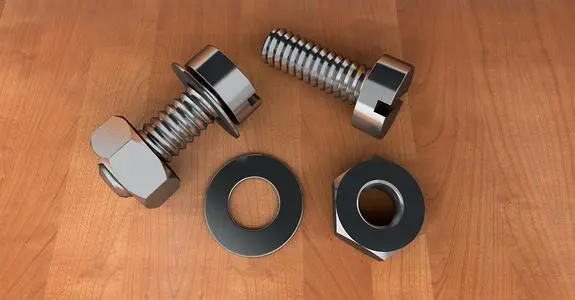
Silver plating, nickel plating
Silver-plated fasteners have good corrosion resistance, smooth surface, lubricating properties, and easy installation. For cost reasons, nuts are silver-plated, bolts are not used, and sometimes small bolts are also silver-plated. Silver loses its luster in the air but can work at 1600 degrees Fahrenheit.
The high-temperature resistance and lubrication characteristics of fasteners that work at high temperatures, silver-plated and nickel-plated fasteners can effectively prevent bolts and nuts from oxidation and jamming.
Fasteners are plated with nickel, which is mainly used in places where anti-corrosion and good conductivity are required. For example, the lead-out terminals of the positive and negative poles on the car battery.
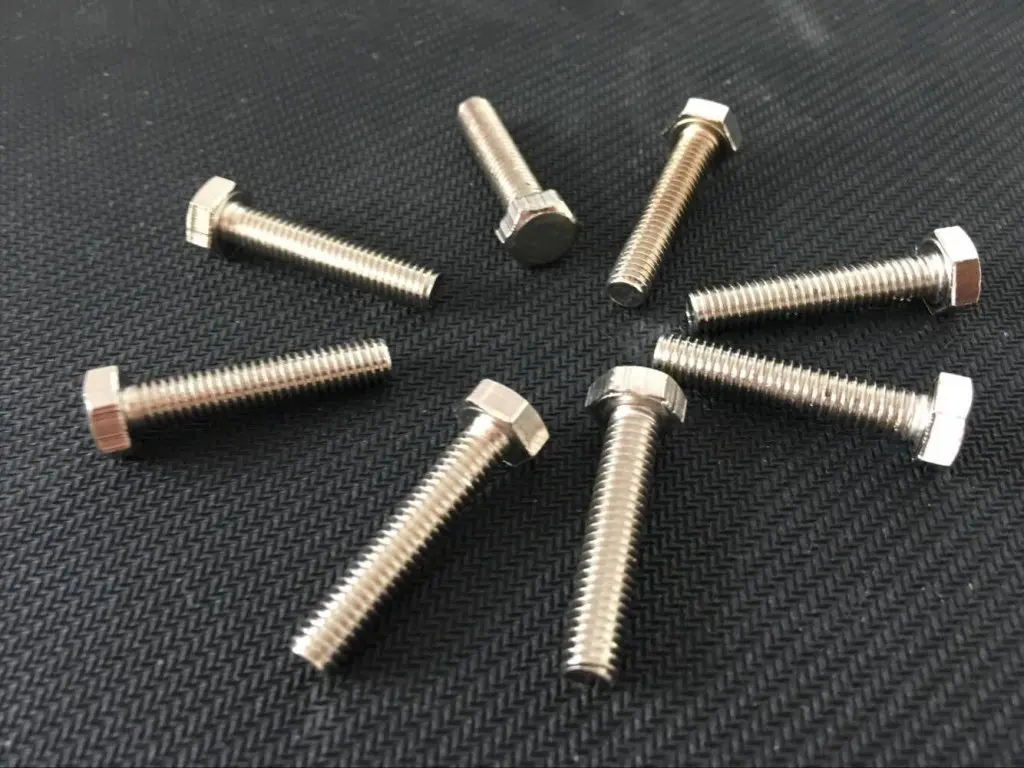
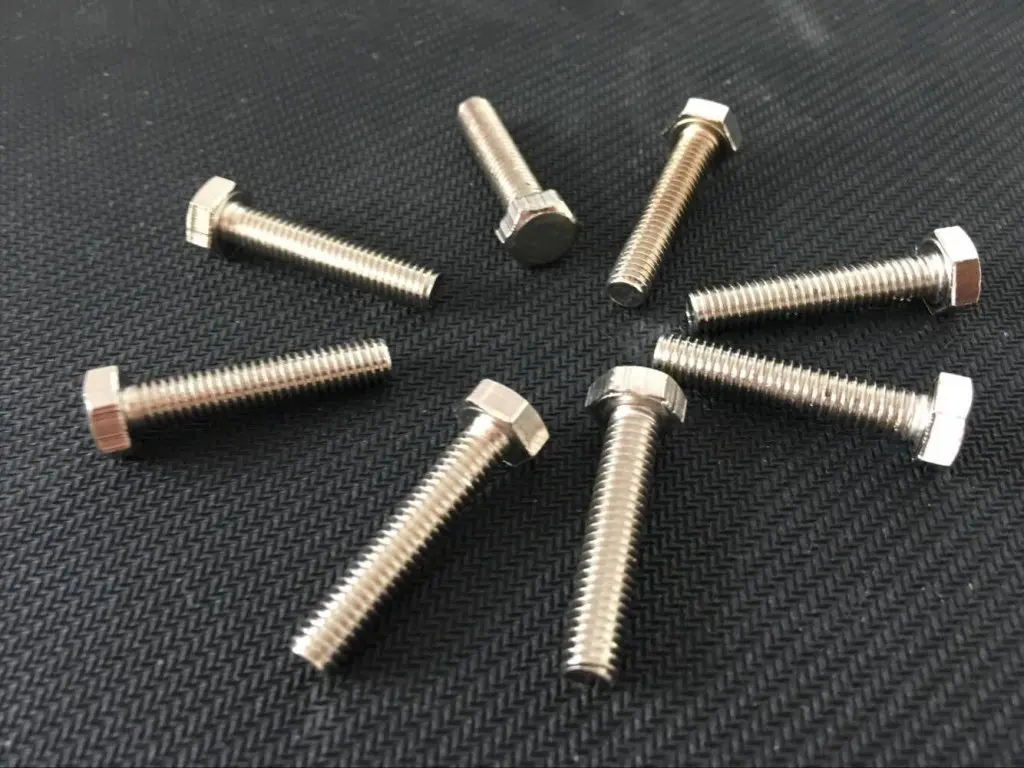
hot-dip galvanized hexagon bolt
Hot-dip galvanizing is zinc heated into the liquid to form a thermal diffusion coating on the surface of the fastener. The thickness of the coating is 15~10μm, and it is not easy to control, but it is corrosive and is mostly used in engineering. During the hot-dip galvanizing process, pollution is serious, such as zinc waste and zinc vapor.
Due to the thick plating layer, it has caused the problem that the internal and external threads are difficult to screw together in the fastener. There are two ways to solve this problem. But it also reduces corrosion resistance. One is to make the thread larger than the standard pattern by about 0.16~0.75mm (M5~M30) when tapping the nut, and then hot-dip galvanized. Although it can also solve the problem of screwing, it pays the price of strength reduction.
At present, there is a kind of anti-loosening thread-American the “Spiro” internal thread that can solve this problem. Because the internal and external threads have a large tolerance when they are not tightened, they can be used to accommodate thick coatings, so it does not affect the twist ability, while the anti-corrosion performance and strength remain the same and will not be affected.
Due to the temperature of hot-dip galvanizing, it cannot be used for fasteners above 10.9.
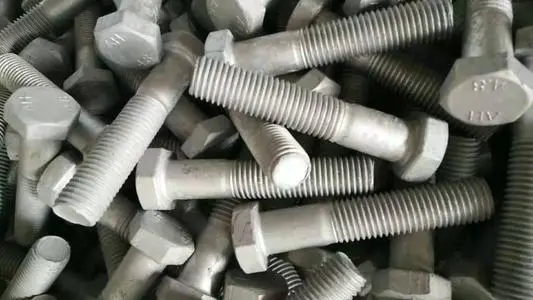
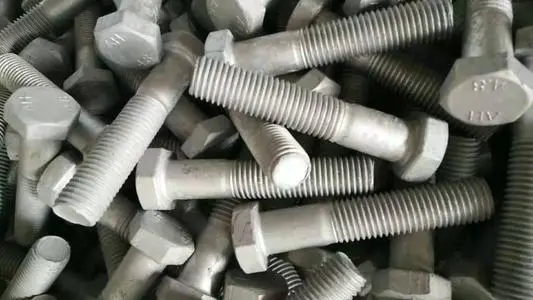
sherardizing
Sherardizing is zinc powder solid metallurgical thermal diffusion coating. Its uniformity is good, and a uniform layer can be obtained in threads and blind holes. The thickness of the coating is 10~110μm, and the error can be controlled within 10%. Its bonding strength and anti-corrosion performance with the substrate are the best among zinc coatings (electro-galvanized, hot-dip galvanized, dacromet). The processing process is pollution-free and environmentally friendly, and it is also the most friendly to the ecological environment
Dacromet
There is no hydrogen embrittlement problem, and the torque-preload consistency performance is very good. If the environmental issues of hexavalent chromium are not considered, it is actually the most suitable for high-strength fasteners with high anti-corrosion requirements.
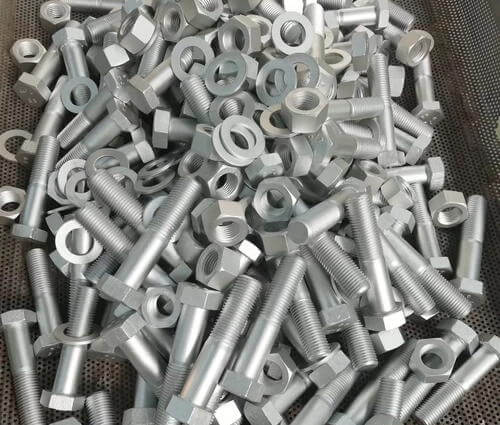
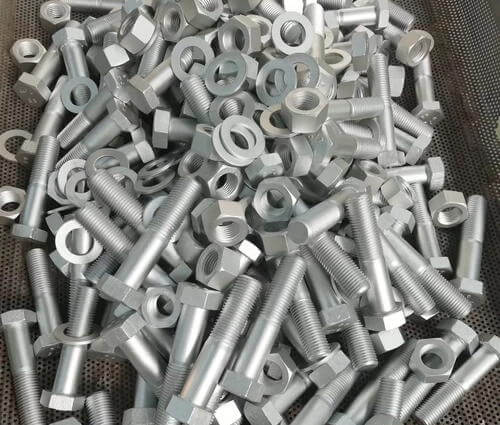